How to Select Aggregate for Concrete Mixing
Concrete mixing requires cement, aggregate, water and admixture. Aggregates include coarse aggregates such as pebbles, gravel, etc., as well as fine aggregate sandstone. Aggregate plays a role in concrete as a skeleton or filled granular loose material. When using concrete mixing plant equipment for commercial concrete production, the choice and proportion of raw materials is important.
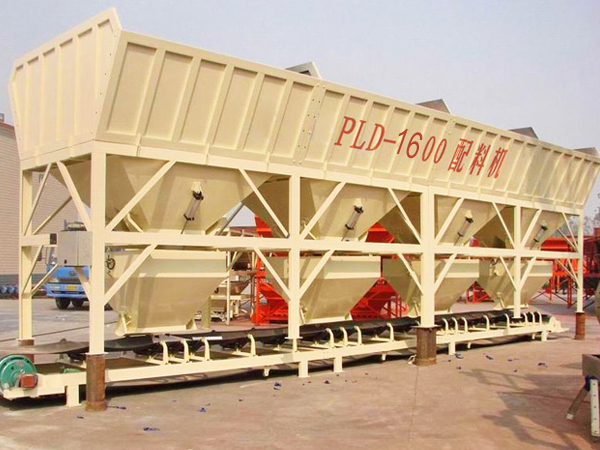
When the stone strength is the same, the surface area of the gravel is larger than that of the pebbles, and its adhesion to the cement mortar is stronger than that of the pebbles. Therefore, gravel is often used as a coarse aggregate required for commercial concrete mixing during construction. However, the specific ratio should be controlled within a reasonable range, so that the concrete has higher volume stability and durability, and reduces the adverse effects such as heat generation and shrinkage of the cement paste.
The selection of fine aggregate should be preferred to use coarse and medium river sand as well. The fine sand is finer and the content of the particles is much. When the water-cement ratio is the same, the cement used for the fine sand mixing commercial concrete is more, the compressive strength is also lowered, and the anti-freezing and anti-wear properties are also poor.
The selection of aggregate requires sufficient strength and compact texture; then it must be clean enough to meet the relevant standards. In addition, the particle size of the aggregate should be appropriate, the appearance also affects the workability of the mixture and the strength of the concrete. The rough-concrete aggregated concrete has poorer workability and higher strength; while the smooth surface of the aggregate has poor adhesion to cement, and the mixed commercial concrete has good workability, but the strength is slightly lower.